Condensate Management
Condensate management in compressed air systems is a critical aspect of maintaining the efficiency and longevity of the system. As compressed air cools down in the pipes, moisture in the air condenses into water. If not managed properly, this condensate can cause several issues, such as corrosion, equipment damage, reduced air quality, and operational inefficiencies.
1. Formation of Condensate
-
When air is compressed, its temperature rises. Upon cooling, moisture in the compressed air condenses and forms liquid water.
-
The amount of condensate depends on the ambient humidity and temperature, the pressure of the compressed air, and how much moisture is in the air.
2. Risks of Improper Condensate Management Corrosion:
-
Moisture in the air can lead to rust and corrosion inside pipes, valves, and equipment.
-
Reduced Efficiency: Water in the system can cause blockages and restrict airflow, reducing system efficiency.
-
Damage to Tools and Equipment: Moisture can damage pneumatic tools, valves, and actuators, leading to malfunction or failure.
-
Air Quality Issues: Condensate can contaminate the air supplied for sensitive processes, such as food or pharmaceutical manufacturing, leading to quality problems.
3. Methods of Condensate Management
Condensate Drainage
-
Manual Drains: These require regular inspection and manual removal of condensate. While cost-effective, they are labour-intensive and prone to human error.
-
Automatic Drains: These are installed to automatically remove condensate at regular intervals. They can be based on timers or sensors that detect moisture.
-
Float-Activated Drains: These use a float to detect when a certain water level has been reached and then open the drain valve.
-
Electronic Drains: These use electronic sensors to detect moisture in the system and open the valve to discharge the condensate when needed.
Air-Line Filters & Dryers
-
Air Filters: These remove large particles and contaminants from the compressed air, which can also capture some of the moisture.
-
Refrigerated Air Dryers: These cool the air down to a point where moisture condenses and is removed from the system. They are widely used in many applications but can increase energy consumption.
-
Desiccant Dryers: These use materials that absorb moisture from the air, providing very low dew points suitable for applications requiring dry air.
-
Membrane Dryers: These work by passing air through a semi-permeable membrane, allowing moisture to be removed from the compressed air.
Condensate Separators
-
These devices are used to separate liquid water from compressed air before the condensate reaches the drainage system. They help to minimize the amount of condensate released into the environment and reduce maintenance on drains.
Proper Piping Design
-
Proper design of the compressed air system’s piping can help prevent condensate accumulation. Pipes should have a slight downward slope towards drains to allow gravity to assist in the removal of condensate.
Collection and Disposal of Condensate
-
Oil-Water Separators: In systems where compressed air may be contaminated with oil (e.g., from compressors), condensate must be treated before disposal. Oil-water separators ensure that only clean water is released into the environment, following local disposal regulations.
-
Environmental Impact Consideration: Properly managing and disposing of condensate is important for environmental sustainability. Condensate should not be dumped directly into drains or the ground, especially if it contains oil or other contaminants.
4. Best Practices for Condensate Management
-
Regular Monitoring: Check condensate drains, filters, and dryers regularly to ensure proper operation.
-
Periodic Maintenance: Keep condensate management equipment like drains and separators well-maintained to avoid failures.
-
Use Proper Drain Sizing: Ensure that the system’s condensate removal system is adequately sized to handle the expected volume.
-
Install Aftercoolers: These help to reduce the temperature of compressed air before it enters the piping system, reducing the amount of condensate formed.


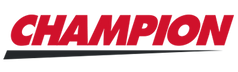

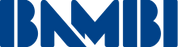


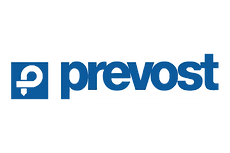